In-Operando vibration analysis of technical systems with Laser Doppler Vibrometry
Structural Health Monitoring (SHM) with Multipoint Vibrometer
State of the art / motivation
- Single-point data acquisition for transient oscillations
- Full-Field data acquisition by 3D Scanning Laser Doppler Vibrometry for steady-state oscillations
Methods
- Additional local resolution via parallel techniques with Multi-Channel Vibrometer for transient oscillations
- Usable oscillation shapes up to 100 kHz from the use of laser excitation
Publications
- X. Cao, C. Rembe:
Non-Contact Damage Detection under Operational Conditions with Multipoint Laservibrometry.
In: sensors (Special Issue: Full-Field Optical Measurement Techniques for Damage Assessment). Vol. 20, Issue 3, 732, Jan. 2020.
DOI: 10.3390/s20030732 - X. Cao, B. Tarigan, C. Rembe and H. Schwarze:
Vibration-based white etching cracks detection at rolling contact bearings.
In: tm - Technisches Messen. Vol. 85, Issue 6, pp. 443-453, June 2018.
DOI: 10.1515/teme-2017-0141 - X. Cao, B. Tarigan, H. Schwarze and C. Rembe:
Damage Identification at rolling contact bearings.
In: tm - Technisches Messen. Vol. 84, Issue s1, pp. 34-41, Sept. 2017.
DOI: 10.1515/teme-2017-0029
Planar vibration measurement with Laser Doppler Vibrometry
State of the art / motivation
- Industrial Scanning Laser Doppler Vibrometer
- Robot-controlled 3D Scanning Laser Doppler Vibrometer
Methods
- Alternative solution by combination of a 1D Laser Doppler Vibrometer and an industrial robot
- Deployment of Multi-Channel Vibrometry
Research results
- 3D Scanning Vibrometer, realized with a single-point head and a robot, can be used flexibly for oscillations up to 23 kHz.
- Influence of specifically placed welding seams on oscillation power and attenuation can be measured with this Vibrometer Robot System.
Publications
- X. Cao, R. Schmelter, T. Ziemer, A. Lohrengel and C. Rembe:
Analyse von Plattenschwingungen mit einem robotergesteuerten 1D Vibrometer zur Charakterisierung des Einflusses lokaler Materialinhomogenitäten.
In: Fakultät für Mathematik/Informatik und Maschinenbau, Technische Universität Clausthal (Hrsg.): Technical Report Series. Fac3-16-02. Oct. 2016.
Investigation and optimization of structure-borne sound transmission in technical systems
State of the art / motivation
- Method of characterizing structure-borne sound for SDOF- and MDOF-coupled systems
- Lack of a method for areal-coupled systems
Research activity
- Mapping of the system with finite element model and adjustment of the model parameters with model updating procedures using the measurement data from the full field vibration measurement
- Calculation of the structure-borne sound transmission in the system using the adjusted model
- Optimization of the structure-borne sound properties of the system using the FE model
Research results
- Structure-borne sound energy flow on structures joined by bolted connections must be simulated with high resolution using FEM models.
- FEM models must be adapted to the physical reality via model updating procedures in order to determine the energy flow correctly.
Publications
- X. Cao, S. Backhaus, R. Scheidl and C. Rembe:
Numerical and Experimental Analysis of structure-borne Sound Transmission in Coupled Systems.
In: Proceedings of the 12th Int. Conference on Vibration Measurements by Laser and Noncontact Techniques, Ancona, Italy, 2016.
DOI: 10.1063/1.4952681 .
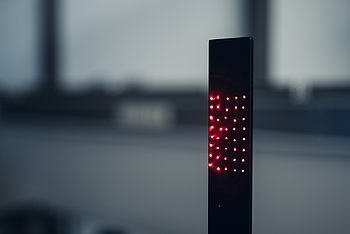
Tel.: +49 5323 72-2126
E-Mail: cao@iei.tu-clausthal.de