Contactless Interferometric Strain measurement
State of the art / Motivation
- Conventional strain measurement with strain gauges:
- Measuring errors due to contact (adhesives)
- Sensitive towards strain perpendicular to the measuring direction
- Influences of temperature at the measuring location
- Complex measuring set-up with several measuring points
- Current optical contactless strain sensors, e.g. Digital Image Correlation (DIC)
- Low sampling rate
- Higher noise
- No electrical real-time measurement due to post-processing
Methods
- Sensor principle of in-plane Laser Doppler Vibrometry transferred to strain measurement
- A stripe pattern is generated by two laser beams crossing each other on the measuring surface. The movement of the scattering body through the stripe pattern forms the intensity modulation, whose frequency is proportional to the velocity perpendicular to the stripe. In-plane deflection of each measurement point is proportional to the integration of the frequency. The strain results from the difference of the deflection at two measuring points in relation to the distance.
Polarization diversity reduces speckle noise and occurrence of the signal dropout
Problem of speckle noise and signal dropouts:
- Low light power due to dark speckle - speckle noise
- Carrier-to-noise ratio (C/N) of the detector signal falls below the frequency modulation threshold (FM threshold) - Signal dropout
- In case of signal dropout, noise > signal power, strain not measurable
Solution of polarization diversity:
- For each measurement point two photodetector detects light in the orthogonal polarization states
- Stochastically independent detector signals
- Probability for simultaneous signal dropouts of both detectors is significantly lower than for a single dropout
Results
- Design of the principle of a novel contactless strain sensor
- Simulation of the optimal sensor setup
- Realization of an experimental setup of the sensor
- Integration of strain sensor in resonance testing machine of SincoTec
- The optical sensor provides comparable measurement results to a strain gauge
State of the art / Motivation
- Strain measurement in high-speed tear testing at a speed of 30 m/s, tear process in only a few ms or µs
- Conventional measurement methods such as strain gauges or speckle correlation not suitable
- Laser Doppler strain sensor with the high spatial and temporal resolution, suitable for high frequency and high speed measurements
Methods
- Laser Doppler strain sensor in a high-speed tensile testing machine by Sincotec GmbH
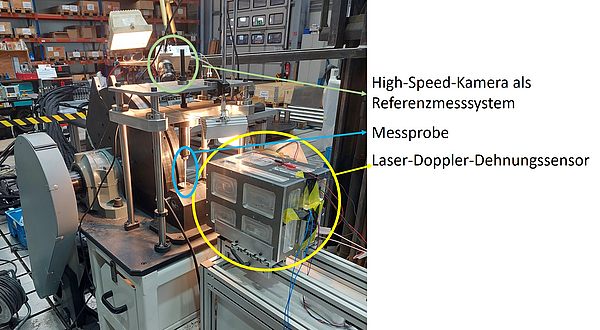
Results
- Implementation of the sensor design with signal diversity. Influence of signal dropout and speckle noise is reduced.
- Improvement of the signal-to-noise ratio (SNR). The high crack speed of 30 m/s requires a very high demodulation bandwidth of the strain sensor. The SNR as well as the resolution is not worse than for strain measurement in fatigue testing despite the very high bandwidth.
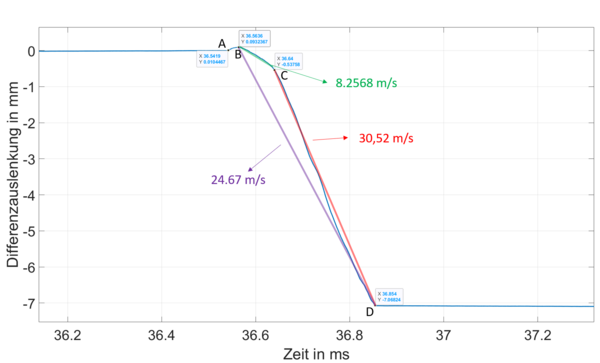
Publications
- F. Wang, S. Krause, und C. Rembe:
Signal diversity for the reduction of signal dropouts and speckle noise in a laser-Doppler extensometer
In: Measurement: Sensors, 2022. DOI: 10.1016/j.measen.2022.100377. - F. Wang, S. Krause, J. Hug and C. Rembe:
A Contactless Laser Doppler Strain Sensor for Fatigue Testing with Resonance-Testing Machine
In: Sensors 2021, 21(1), 319. DOI: 10.3390/s21010319. - F. Wang and C. Rembe:
Kontaktloser interferometrischer Dehnungssensor.
In: Tagungsband 3. Niedersächsisches Symposium Materialtechnik. pp. 51-65, 2019. DOI: 10.21268/20190312-3 - F. Wang and C. Rembe:
Entwurf eines kontaktlosen interferometrischen Dehnungssensors.
In: tm - Technisches Messen. Vol. 85, Issue s1, pp. 117-123, Sept 2018. DOI: 10.1515/teme-2018-0045.
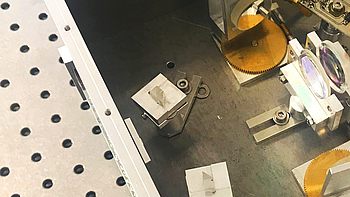